JOHNPEET
Well-known member
Fly bridge decking!
The only way that I felt that I could tackle the fly bridge area was to again, split the area into separate decking mats that I could fabricate and install. The fly bridge isn’t an enormous area by any means, but it has a number of fixed obstacles that I had to work around and I think you’d have to be much better than I am to make it in such a way as to make it appear as if it’s a single sheet/mat.
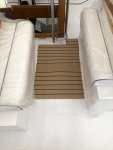
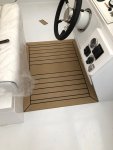
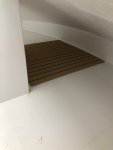
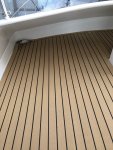
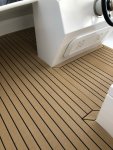
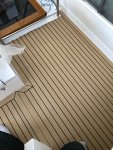
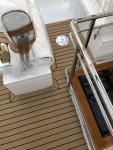
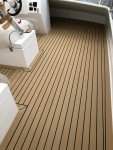
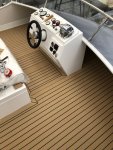
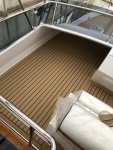
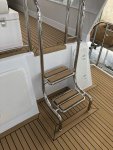
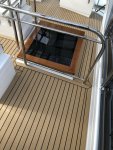
The only way that I felt that I could tackle the fly bridge area was to again, split the area into separate decking mats that I could fabricate and install. The fly bridge isn’t an enormous area by any means, but it has a number of fixed obstacles that I had to work around and I think you’d have to be much better than I am to make it in such a way as to make it appear as if it’s a single sheet/mat.
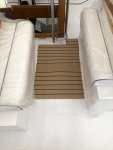
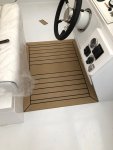
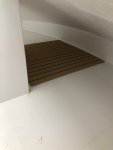
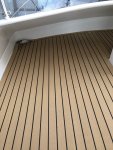
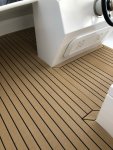
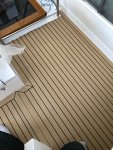
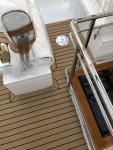
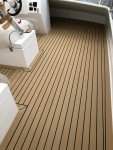
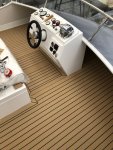
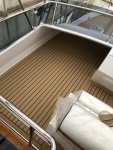
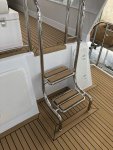
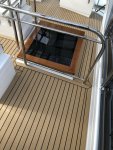