ChasB
Member
Hi,
I need to route a gas pipe out of a box (where the gas bottle sits) down through the GRP double-thickness deck. The deck is 40 - 50mm thick. That's two layers of GRP with balsa between. Really hard to tell exactly how thick this is in total until a hole is made , but it seems to be too long for a copper gas skin fitting. My solution is to fit a plastic skin fitting that goes all the way through which would allow a gas pipe to pass through inside of that with some wiggle room.
Once fitted, sealant would of course have to be applied to fill in the gap around the gas pipe to stop any gas leakeage (or water!) making its way down.
The plastic fitting TruDesign Long Domed Skin Fittings (Thru Hulls) has an outside diameter of 33mm. Once measured up it would be cut to length.
So, I need to make a hole of 34mm dia. through the hull. How would I do this easily, cleanly, cheaply, and without cracks in the hull?
BTW My intention is to fit this plastic thing myself, and leave the gas to a professional.
Many thanks
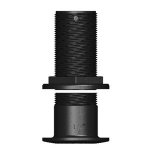
p.s. Since cold things are more inclined to be be brittle, would it help to warm up the area with a heat gun first?
I need to route a gas pipe out of a box (where the gas bottle sits) down through the GRP double-thickness deck. The deck is 40 - 50mm thick. That's two layers of GRP with balsa between. Really hard to tell exactly how thick this is in total until a hole is made , but it seems to be too long for a copper gas skin fitting. My solution is to fit a plastic skin fitting that goes all the way through which would allow a gas pipe to pass through inside of that with some wiggle room.
Once fitted, sealant would of course have to be applied to fill in the gap around the gas pipe to stop any gas leakeage (or water!) making its way down.
The plastic fitting TruDesign Long Domed Skin Fittings (Thru Hulls) has an outside diameter of 33mm. Once measured up it would be cut to length.
So, I need to make a hole of 34mm dia. through the hull. How would I do this easily, cleanly, cheaply, and without cracks in the hull?
BTW My intention is to fit this plastic thing myself, and leave the gas to a professional.
Many thanks
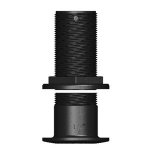
p.s. Since cold things are more inclined to be be brittle, would it help to warm up the area with a heat gun first?
Last edited: