OldBawley
Active member
Only for Mechanics.
New oil cooler for gearbox
The oil cooler for our Paragon transmission is at its end. Electrolysis holed the brass cooler mantle on a few places. Hairpin holes in the brass leak minute quantity's of ATF oil, wont be long before the oil pressure will kill the cooler.
The bowman heat exchanger of the Perkins 4108 had electrolysis problems too, so when I discovered a small heat exchanger on a pile of metal junk next to a Greek garage I bought it for 10 €.
I discovered the pinholes a week ago, now I have time to repair. Digged the second hand cooler out of half a ton of spares, and was lucky. The new cooler is a bit bigger but has the same thread as the old one for the oil pressure hoses. Thank God. The connections for the seawater hoses are bigger, so I had to improvise.
Hose inside diameter 32 mm, cooler connection 43 mm. To big a difference for a flexible hose.
Main problem is my location. Sailing in Greece means getting material is difficult if not impossible.
Second problem is that those oil coolers are soldered together in a stepped way, maybe even with different types of solder for each weld. That means no soldering or welding on the cooler or it will leak and or fall apart.
So I decided to glue brass inserts into the cooler.
See sketch
The new old cooler had been used to cool a small engine. Where I want to cool hydraulic oil, they had been cooling anti freeze . So I cleaned the inside as good as possible with caustic soda ( Drain cleaner ) and hot water.
I have a small hobby lathe on board so theoretical I could turn brass bushings to fit into the cooler en take the water hoses. Again Greece, so no way to buy brass except for one shop in Pireaus.
To far out of my way so I bought two brass trough hull fittings in the local farmers shop. One fifth of the price a chandler wants.
Now the flange of the trough hull is made a tight fit with the bore of the cooler. That way both are centred. Then I want to use ordinary Polyurethane glue / sealant ( Sicaflex ) to glue the trough hull inside the cooler. About 3/ 64 “ clearance between cooler and trough hull, which is fine I think.
Then I want to fill the thread of the trough hull where it takes the hose with the same polyurethane to prevent water leaking trough the tread.
Last thing to do is mount the cooler with a sheet of isolating rubber so no stray electrical current can flow.
Now up to the mechanics, what did I do wrong ?
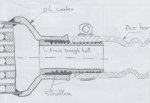
New oil cooler for gearbox
The oil cooler for our Paragon transmission is at its end. Electrolysis holed the brass cooler mantle on a few places. Hairpin holes in the brass leak minute quantity's of ATF oil, wont be long before the oil pressure will kill the cooler.
The bowman heat exchanger of the Perkins 4108 had electrolysis problems too, so when I discovered a small heat exchanger on a pile of metal junk next to a Greek garage I bought it for 10 €.
I discovered the pinholes a week ago, now I have time to repair. Digged the second hand cooler out of half a ton of spares, and was lucky. The new cooler is a bit bigger but has the same thread as the old one for the oil pressure hoses. Thank God. The connections for the seawater hoses are bigger, so I had to improvise.
Hose inside diameter 32 mm, cooler connection 43 mm. To big a difference for a flexible hose.
Main problem is my location. Sailing in Greece means getting material is difficult if not impossible.
Second problem is that those oil coolers are soldered together in a stepped way, maybe even with different types of solder for each weld. That means no soldering or welding on the cooler or it will leak and or fall apart.
So I decided to glue brass inserts into the cooler.
See sketch
The new old cooler had been used to cool a small engine. Where I want to cool hydraulic oil, they had been cooling anti freeze . So I cleaned the inside as good as possible with caustic soda ( Drain cleaner ) and hot water.
I have a small hobby lathe on board so theoretical I could turn brass bushings to fit into the cooler en take the water hoses. Again Greece, so no way to buy brass except for one shop in Pireaus.
To far out of my way so I bought two brass trough hull fittings in the local farmers shop. One fifth of the price a chandler wants.
Now the flange of the trough hull is made a tight fit with the bore of the cooler. That way both are centred. Then I want to use ordinary Polyurethane glue / sealant ( Sicaflex ) to glue the trough hull inside the cooler. About 3/ 64 “ clearance between cooler and trough hull, which is fine I think.
Then I want to fill the thread of the trough hull where it takes the hose with the same polyurethane to prevent water leaking trough the tread.
Last thing to do is mount the cooler with a sheet of isolating rubber so no stray electrical current can flow.
Now up to the mechanics, what did I do wrong ?
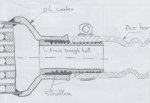