DangerousPirate
Active member
Still thinking about that solar arch haha.
I had a few quotes for solar arch in the meantime, and without anyone even looking yet the quotes started way above my budget, 6k and up.
Thinking of doing it myself now. I thought of getting bimini fittings and fiddle together an overhanging design. There obviously won't be any welding or tube bending for that matter only straight tubes and whatever I can do with the fittings.
1. Now I noticed from the many videos on the subject that most archs don't seem to have a 90° angle on the x-axis (front to back), rather more like 110° or so and wonder if there is a specific reason for that?
And I need to hang it over the stern otherwise my backstay will be in the way as it's a dual backstay (adjustable) and kind of central.
2. How sturdy are those bimini connectors? Would that hold up or bad idea?
3. Is welding/bending necessary or is that just for looks?
4. What kind of steel should I use, what thickness is enough?
5. Aluminium as an alternative? Strong enough?
Has anyone gone down this route?
For anyone interested: I got a Camper Nicholson 30.
The idea is to make it look somewhat like this picture, that I found online: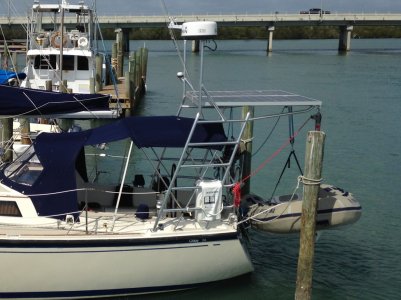
I know this is an expensive job, as they welded and have integrated it into the pushpit, but the idea is about the same. Maybe with, maybe without the dinghy davit. Not sure. Depends on how sturdy it can be in the end.
I had a few quotes for solar arch in the meantime, and without anyone even looking yet the quotes started way above my budget, 6k and up.
Thinking of doing it myself now. I thought of getting bimini fittings and fiddle together an overhanging design. There obviously won't be any welding or tube bending for that matter only straight tubes and whatever I can do with the fittings.
1. Now I noticed from the many videos on the subject that most archs don't seem to have a 90° angle on the x-axis (front to back), rather more like 110° or so and wonder if there is a specific reason for that?
And I need to hang it over the stern otherwise my backstay will be in the way as it's a dual backstay (adjustable) and kind of central.
2. How sturdy are those bimini connectors? Would that hold up or bad idea?
3. Is welding/bending necessary or is that just for looks?
4. What kind of steel should I use, what thickness is enough?
5. Aluminium as an alternative? Strong enough?
Has anyone gone down this route?
For anyone interested: I got a Camper Nicholson 30.
The idea is to make it look somewhat like this picture, that I found online:
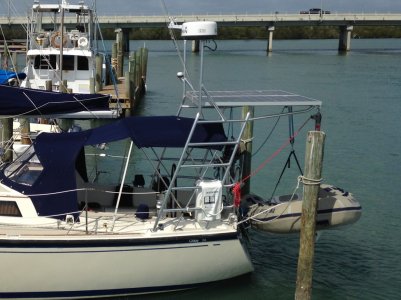
I know this is an expensive job, as they welded and have integrated it into the pushpit, but the idea is about the same. Maybe with, maybe without the dinghy davit. Not sure. Depends on how sturdy it can be in the end.