YOYA
New member
Hi
In the process of replacing engine mounts and repacking stuffing box I have disconnected the shaft coupling from the gear.
now that the shaft is disconnected I can see the shaft tube with the attached stuffing box have a slight wiggle of few mm when moved by hand.
the stern tube ends at a small sort of bulkhead or stinger made of wood and covered with glass and mat. forward of it is the stuffing box which has a flange with two bolts going through that bulkhead. the material around the bolts disintegrated. the sealant between the flange and the bulkhed is also loose.
I want to refill this lost material, redrill the holes for the stuffing box flange bolts and reseal or cment the flange to the bulkhead (there are no leaks from the flange / stern tube, just from the stuffing box which needs a new packing)
1) is the flange part of the stern tube or can it and the stuffing box moved forward on the shaft so I can rebuild that bulkhead? I tried to move it but no go so far.
2) how to rebuild the damaged area - use epoxy and mat? epoxy putty? this area is maybe 5x5 cm.
3) this being a vertical area, how do I keep the epoxy in place until it dries? should I create some kind of mold so the epoxy is not going to run down.?
4) the slight movement of the whole assemply - stuffing box, flange, stern tube and shaft - is this normal desired flexibility?
5) I want to do that before I align the engine to the shaft coupling. Should I also repack the stuffing box before alignment?
with a running engine and in gear a slight vibration movement is visible in the flange/stuffing box. no serious woobling in shaft or noticable vibrations in the boat. The engine mounts were due to be replaced.
Westerly Conway 36 1979 currently on the dry
many thanks for your input
top view of stuffing box
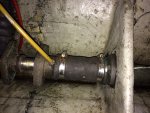
aft area of bulkhead
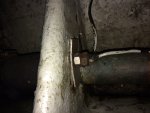
shaft + empty stuffing box
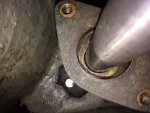
rotten area in bulkhead under stuffing box flange with bolts removed
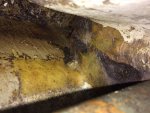
In the process of replacing engine mounts and repacking stuffing box I have disconnected the shaft coupling from the gear.
now that the shaft is disconnected I can see the shaft tube with the attached stuffing box have a slight wiggle of few mm when moved by hand.
the stern tube ends at a small sort of bulkhead or stinger made of wood and covered with glass and mat. forward of it is the stuffing box which has a flange with two bolts going through that bulkhead. the material around the bolts disintegrated. the sealant between the flange and the bulkhed is also loose.
I want to refill this lost material, redrill the holes for the stuffing box flange bolts and reseal or cment the flange to the bulkhead (there are no leaks from the flange / stern tube, just from the stuffing box which needs a new packing)
1) is the flange part of the stern tube or can it and the stuffing box moved forward on the shaft so I can rebuild that bulkhead? I tried to move it but no go so far.
2) how to rebuild the damaged area - use epoxy and mat? epoxy putty? this area is maybe 5x5 cm.
3) this being a vertical area, how do I keep the epoxy in place until it dries? should I create some kind of mold so the epoxy is not going to run down.?
4) the slight movement of the whole assemply - stuffing box, flange, stern tube and shaft - is this normal desired flexibility?
5) I want to do that before I align the engine to the shaft coupling. Should I also repack the stuffing box before alignment?
with a running engine and in gear a slight vibration movement is visible in the flange/stuffing box. no serious woobling in shaft or noticable vibrations in the boat. The engine mounts were due to be replaced.
Westerly Conway 36 1979 currently on the dry
many thanks for your input
top view of stuffing box
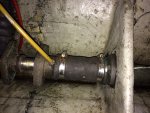
aft area of bulkhead
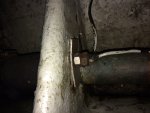
shaft + empty stuffing box
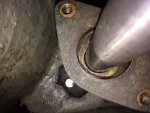
rotten area in bulkhead under stuffing box flange with bolts removed
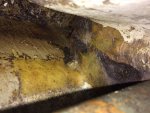