Overandunder
Member
I have recently bought an awb in the form of a Jenny SO 29.2 (2006). As the history of the rigs maintenance is somewhat murky I'm in the process of replacing it.
All straightforward enough - until I came across the forestay attachment point on the alloy stem fitting. I can't use the rearward point as the fitting for the furler wouldn't clear the deck at that point.
So the question is - can I (carefully and accurately) simply drill a new 10mm hole in between both points ? I realise the better solution would be wholesale replacement in stainless - but I'm after a simple and easy fix, albeit 'temporary'
Thanks all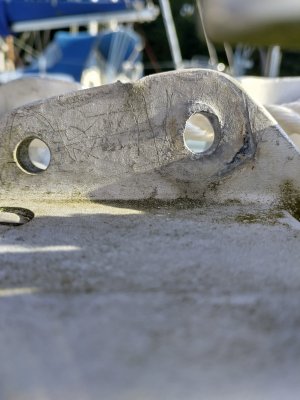
All straightforward enough - until I came across the forestay attachment point on the alloy stem fitting. I can't use the rearward point as the fitting for the furler wouldn't clear the deck at that point.
So the question is - can I (carefully and accurately) simply drill a new 10mm hole in between both points ? I realise the better solution would be wholesale replacement in stainless - but I'm after a simple and easy fix, albeit 'temporary'
Thanks all
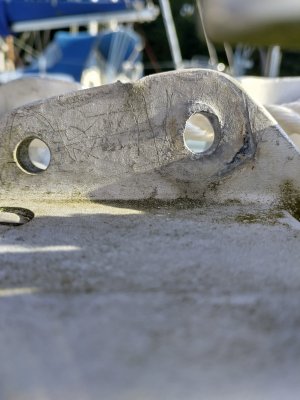