FurryWritingDesk
New member
We had our boat hauled out last week, as part of the toe rail needed replacing. Since then, we seem to have embarked on a rather unpleasant voyage of discovery. A bit of background is probably helpful.
The boat was re-Coppercoated last year. Anodes were replaced. She'd been in the same berth for about 18 months, but the level of growth wasn't too bad and the anodes were in ok nick, but sensible to have them replaced.
Last summer, a big MFV (steel hulled) was moved onto our pontoon. It is a liveaboard and is permanently plugged in, and attached to the water supply. We're both moored side on to the pontoon, with our bow pointing towards the MFV. And yes, we do have a galvanic isolator for our boat. We only have her plugged in to shore power when we're on her, and leave her with all systems off.
Last week, the boat came out with a huge amount of growth on her, firmly attached. All the anodes were almost completely eaten. But worst of all, we have severe pitting on the hull, most notably on the bow.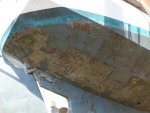
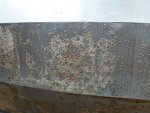
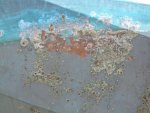
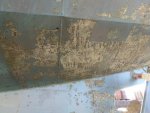
There appear to be some areas of cathodic calcification (I've learnt some new words in the last week).
I would love it if anyone has any thoughts or suggestions as to what we can do or, indeed, what we could have done differently.
We seem to be facing the prospect of having her blasted back to bare steel and starting again, as well as finding a new home for her. None of which is either cheap or particularly convenient.
The boat was re-Coppercoated last year. Anodes were replaced. She'd been in the same berth for about 18 months, but the level of growth wasn't too bad and the anodes were in ok nick, but sensible to have them replaced.
Last summer, a big MFV (steel hulled) was moved onto our pontoon. It is a liveaboard and is permanently plugged in, and attached to the water supply. We're both moored side on to the pontoon, with our bow pointing towards the MFV. And yes, we do have a galvanic isolator for our boat. We only have her plugged in to shore power when we're on her, and leave her with all systems off.
Last week, the boat came out with a huge amount of growth on her, firmly attached. All the anodes were almost completely eaten. But worst of all, we have severe pitting on the hull, most notably on the bow.
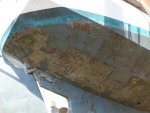
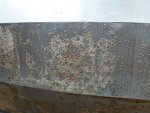
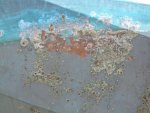
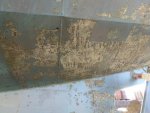
There appear to be some areas of cathodic calcification (I've learnt some new words in the last week).
I would love it if anyone has any thoughts or suggestions as to what we can do or, indeed, what we could have done differently.
We seem to be facing the prospect of having her blasted back to bare steel and starting again, as well as finding a new home for her. None of which is either cheap or particularly convenient.