Vara
Active member
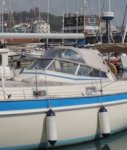
In five years have never folded the thing and it is due for replacement.
What I would like to do is make/have made a fibre glass replacement with window.
How could I take an impression of the hood in situ to enable a replacement to be made.
Or any other ideas for a way forward.
Last edited: