snibble
Member
Hello everyone. Bit of an epic for a first post but like so many I'm on lockdown and bored. I used to sail the solent but not for years and I originally posted this on a canal boat site. It certainly has more relevance here so just for interest here it is.
There's plenty of these things out there although they're a bit antiquated now. I thought I'd go through a rebuild, more for entertainment than information. In fact, it's more likely to put anyone off a DIY job than help!
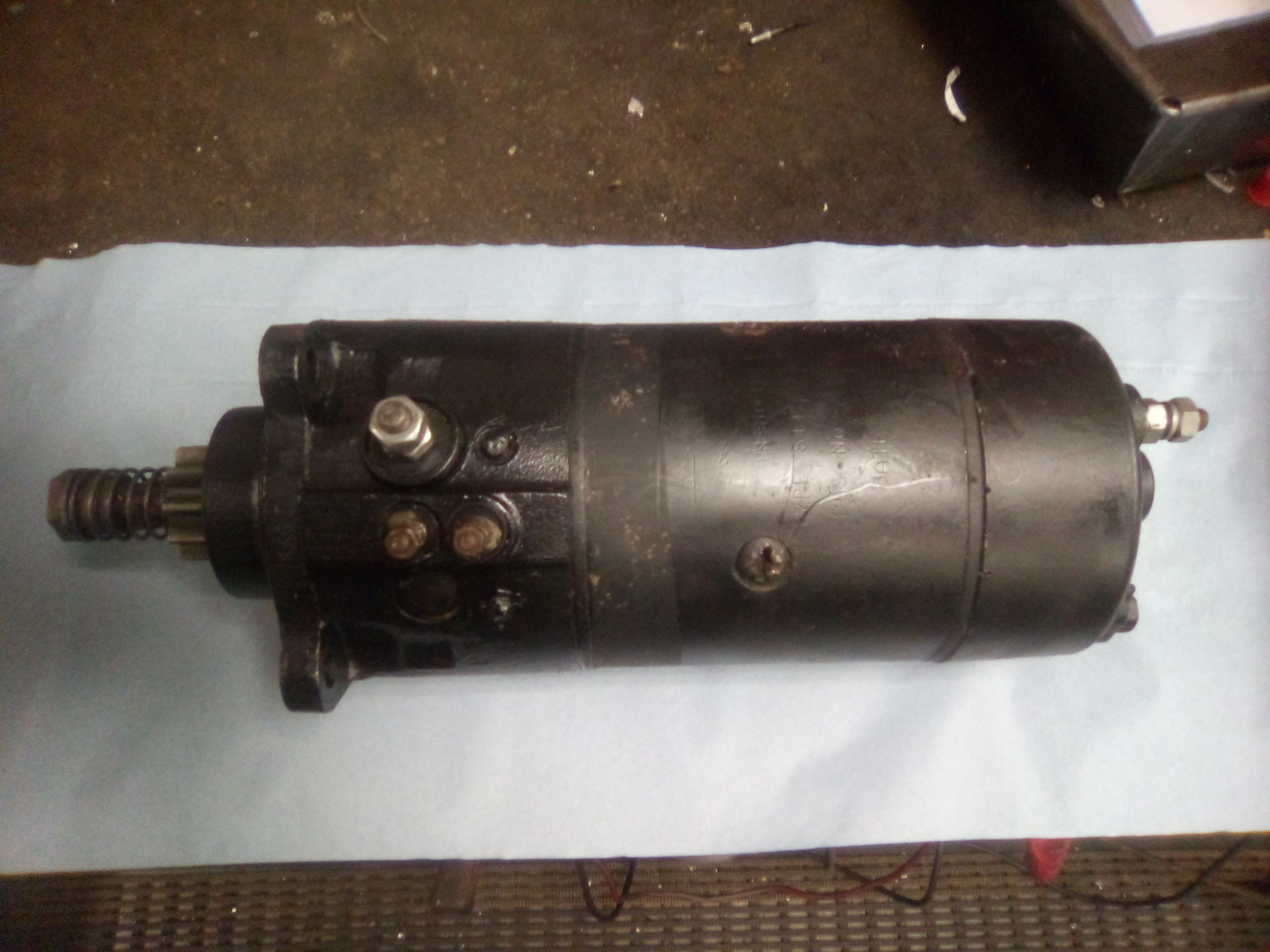
Back end first. Two screws. Behind the cover is a spring loaded ball and a top hat.
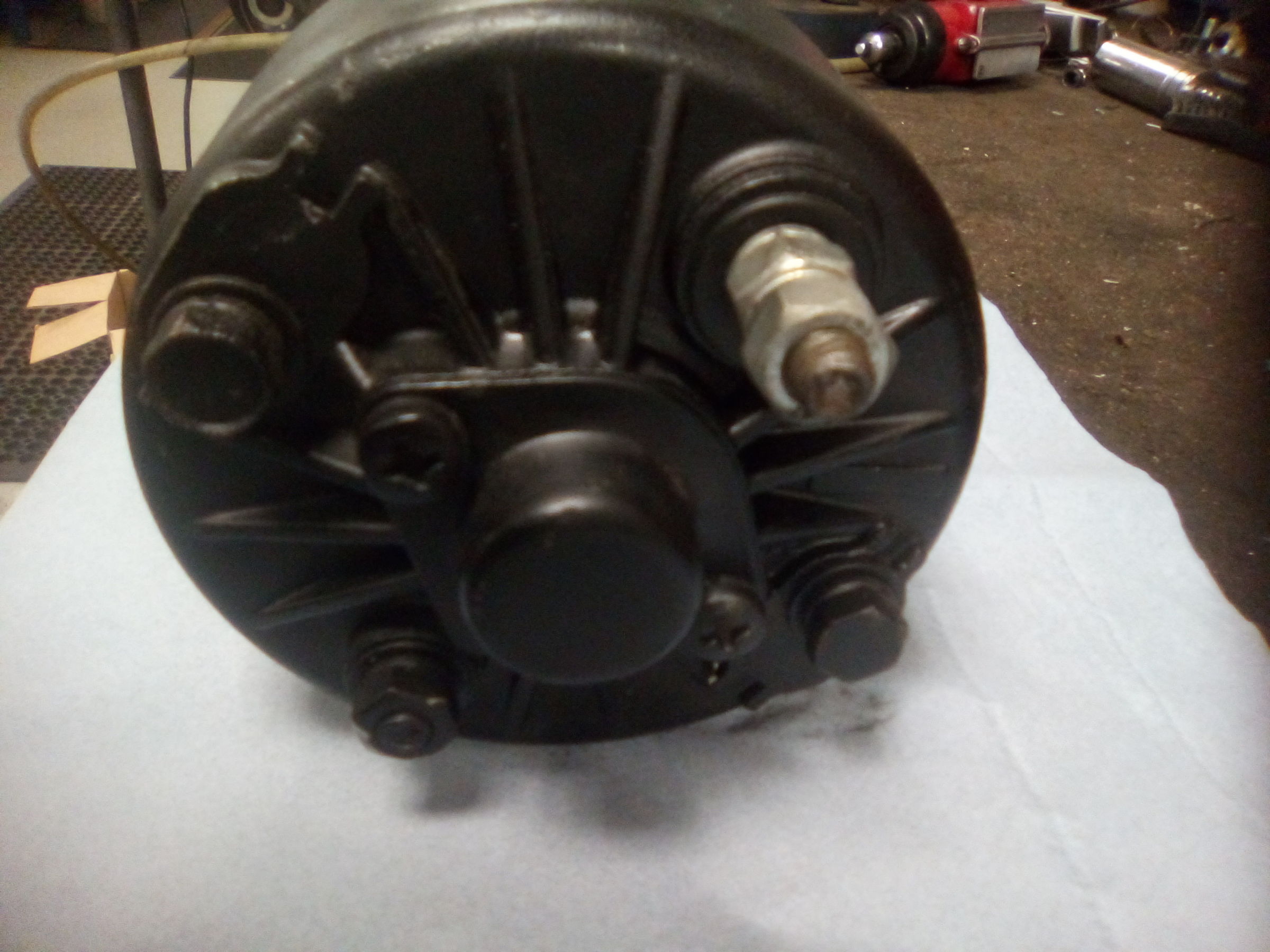
There's also shims to set the end float. I loop a bit of wire through them to keep them together and identify them as being the external group.
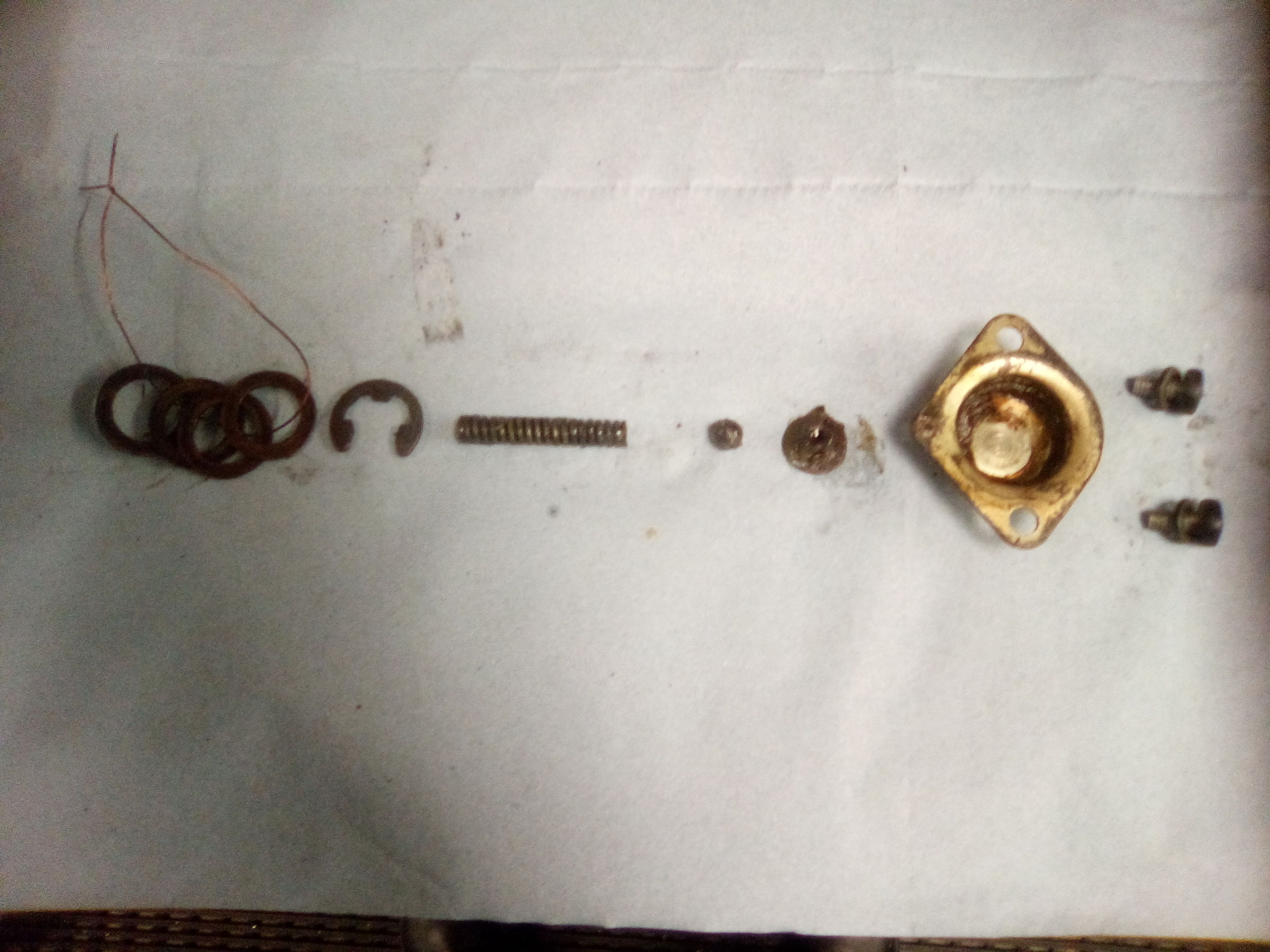
There's plenty of these things out there although they're a bit antiquated now. I thought I'd go through a rebuild, more for entertainment than information. In fact, it's more likely to put anyone off a DIY job than help!
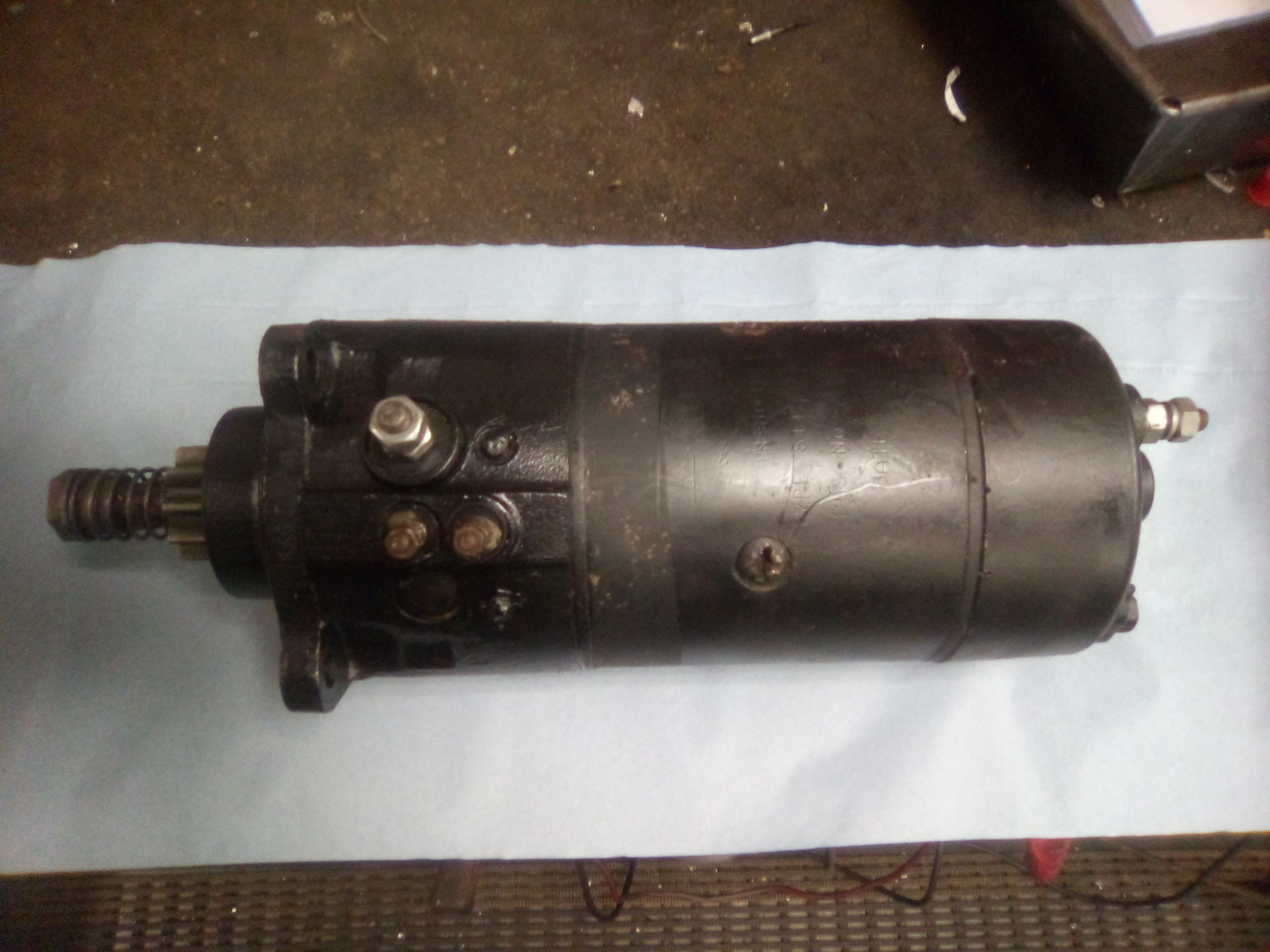
Back end first. Two screws. Behind the cover is a spring loaded ball and a top hat.
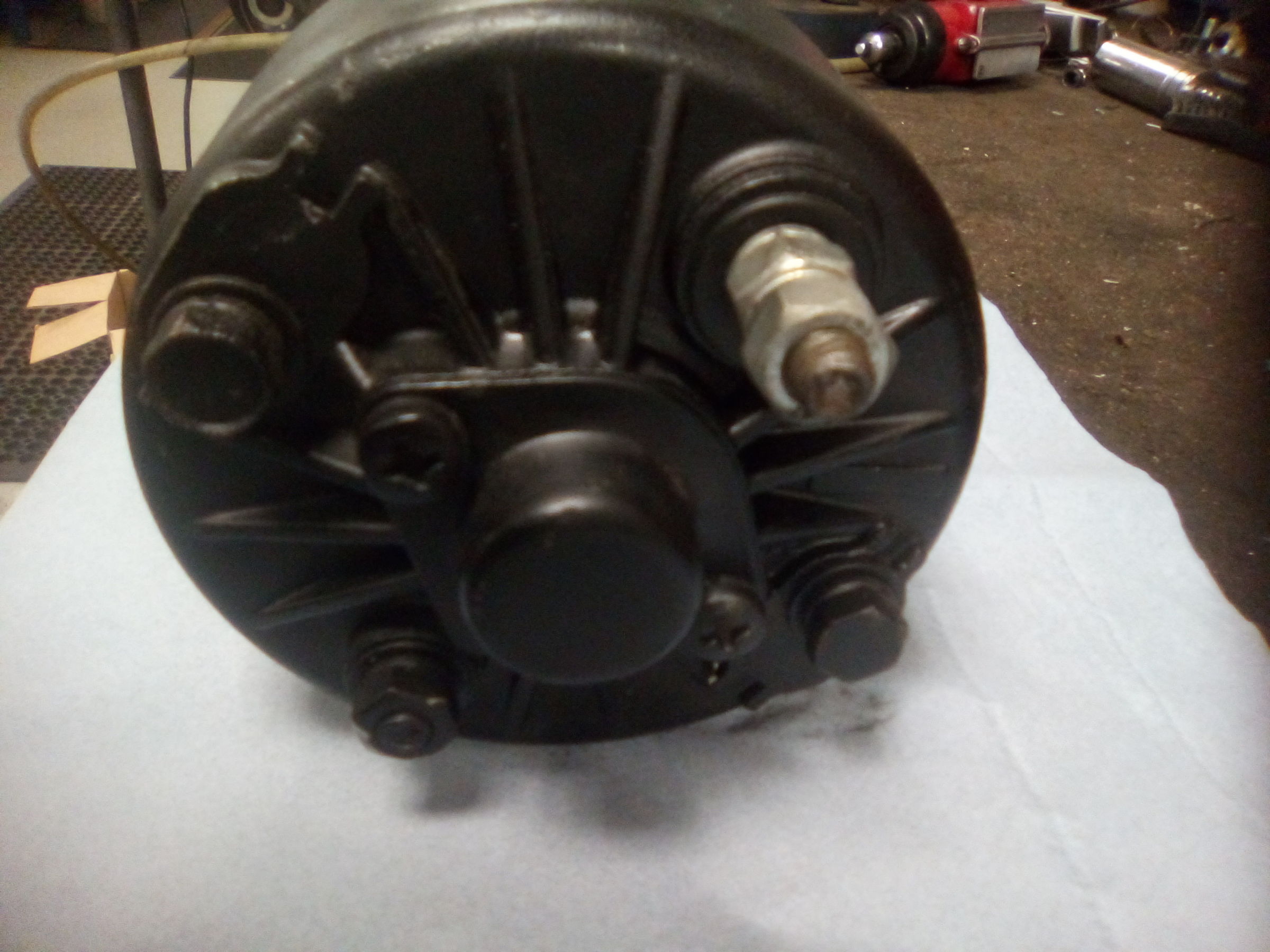
There's also shims to set the end float. I loop a bit of wire through them to keep them together and identify them as being the external group.
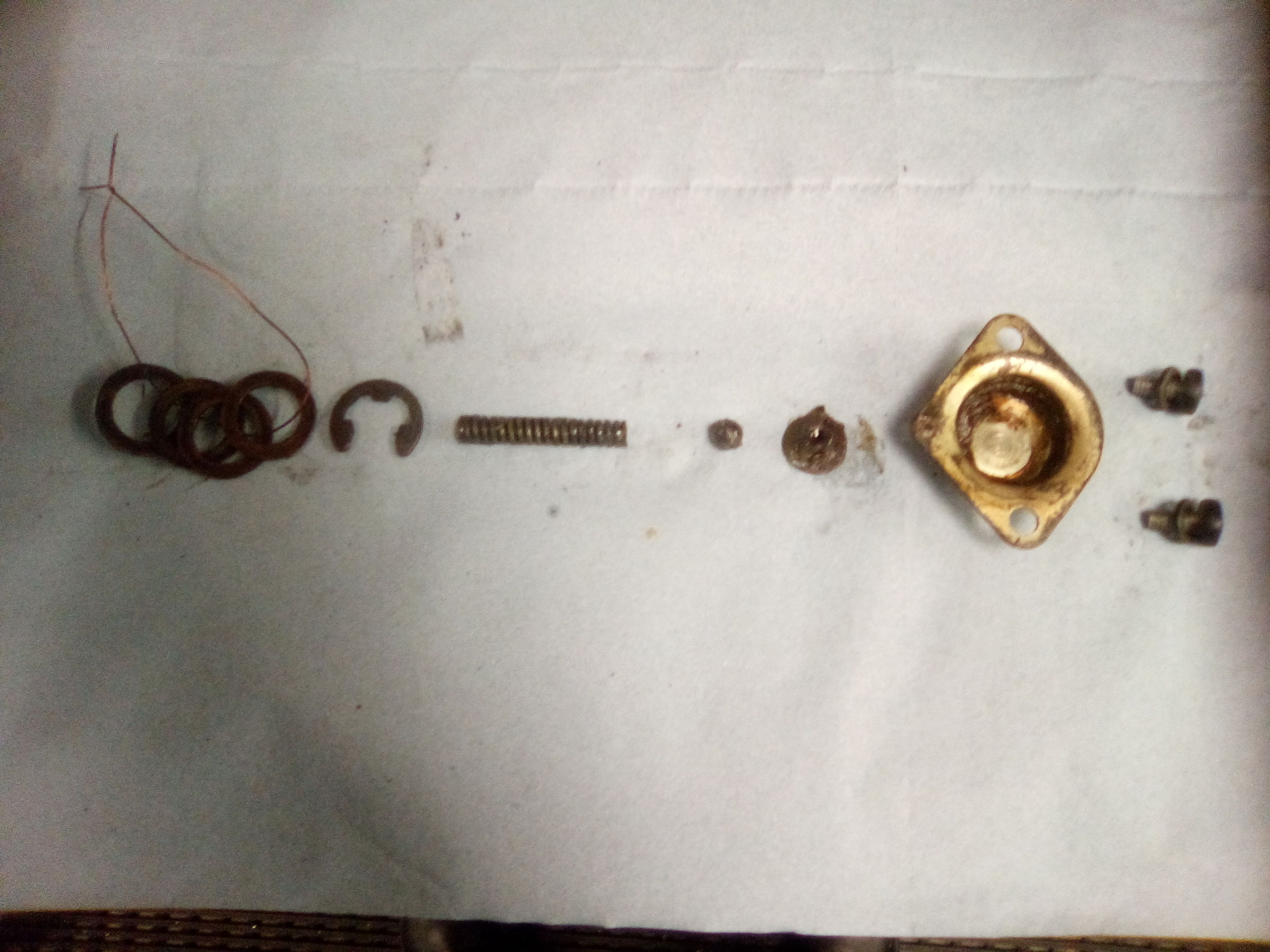