ianc1200
Well-known member
I'm doing a major rebuild of my estuary cruiser, Straight Across. She is a 30' version of the ARC Marine Everyman design, built in Littlehampton in 1951. We have owned her 40 years in December, my grandfather also owned her 1956 - 1974. This is the third time in our ownership we have taken her apart, although the two previous times were on the Thames at Hurley, with the work done by Peter Freebody. She is now in NE Essex at Titchmarsh Marina, Walton on the Naze. As an aside she is about 100 yards away from where Simon is rebuilding Chance/Token. We only restarted in earnest a couple of weeks ago and are having an interesting time. My intention, having done this before and not wanting to end up with rotten oak in a few years, is to replace the steamed oak timbers with laminated iroko - using iroko I had left over from the 2002/3 rebuild. Whilst this might sound simple, what we found was the timbers ot only curved downwards, but also forwards. The 1/4" iroko bent following the shape of the hull, but cracked when we attempted to twist forwards. We then steam bent some oak in, with the intention of reverting to laminated iroko further back. Today we had a go at steaming the laminations, made much easier to get in but also noticed a third complication - the laminations really should be tapered to match the hull such that there is a gap at the aft end of the laminations. Hoping to learn & get right the more we do. To steam we're using a timber long box and a wallpaper steamer - appears to work. The laminations mainly aren't in the correct place, today trying to get some pre bend in them.
.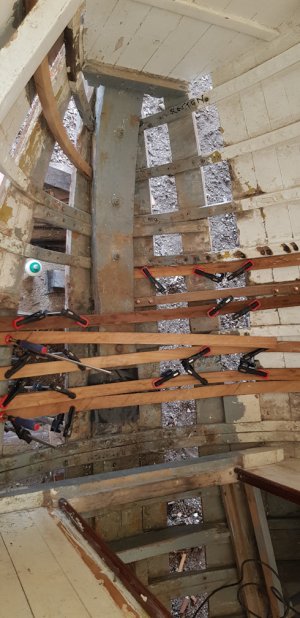

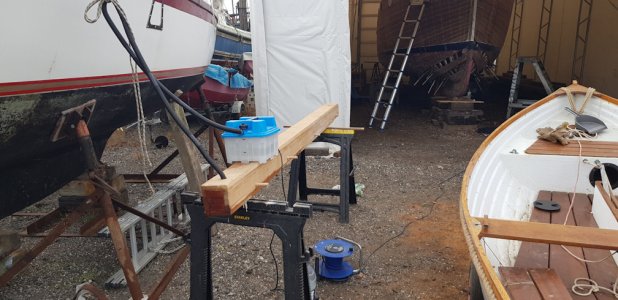
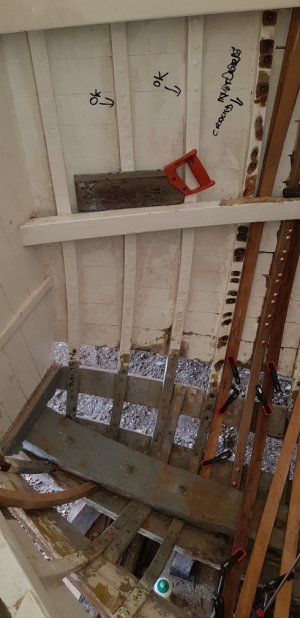
.
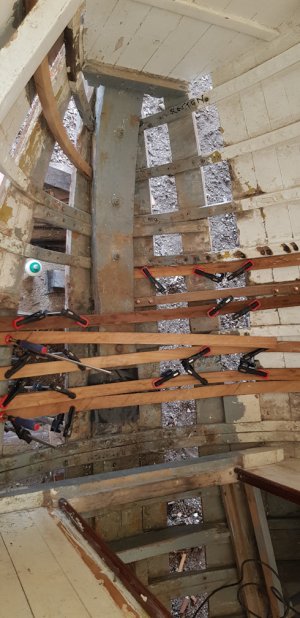

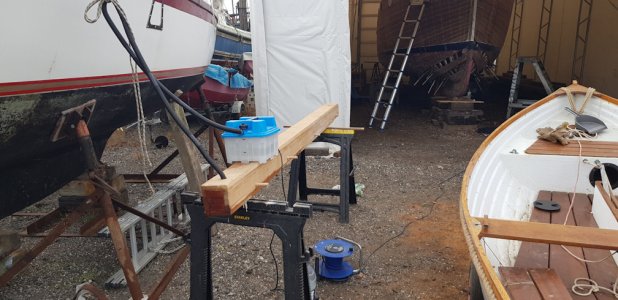
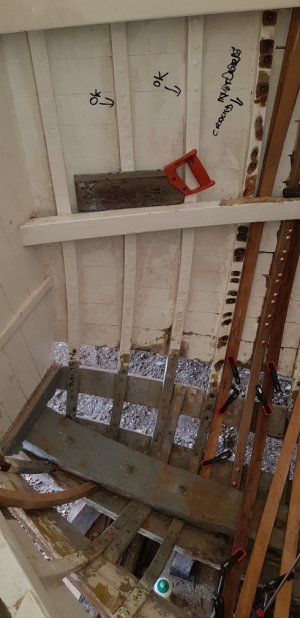