Ian_Edwards
Well-known member
I'm in Australia at the moment avoiding the worst of the Aberdeen winter.
Trying to remove to mast heel casting from a 50year old mast. The mast is off a Cousair sailing dinghy, built by de Havilland, and originally used to train recruits in the Australian Navy.
The heal is held fast by Aluminum to Aluminum corrosion.
The pop rivet has holding it has been drilled out
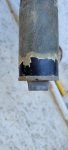

I've tried boiling water and a cold chisel + big hammer, but can't get it to move.
Any ideas on how to soften the corrosion which is gluing the casting into the extrusion.
Classically I'd try vinegar. But it hard to see how the vinegar can be effective, there's very little surface area for it to react with.
The mast is off the boat and in the garage, so I have access to mains power.
Trying to remove to mast heel casting from a 50year old mast. The mast is off a Cousair sailing dinghy, built by de Havilland, and originally used to train recruits in the Australian Navy.
The heal is held fast by Aluminum to Aluminum corrosion.
The pop rivet has holding it has been drilled out
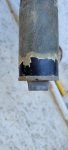

I've tried boiling water and a cold chisel + big hammer, but can't get it to move.
Any ideas on how to soften the corrosion which is gluing the casting into the extrusion.
Classically I'd try vinegar. But it hard to see how the vinegar can be effective, there's very little surface area for it to react with.
The mast is off the boat and in the garage, so I have access to mains power.