chris-s
Well-known member
I've printed absolutely loads of parts! To name a few...
. Various switch mounts/plates
. Crockery, mug and storage container racks which can be stacked to make use of space
. Mounting brackets for things like the EDF1, the NASA LED mast top light and more
. Handheld VHF bracket
. Deck hardware standoffs
. Shaped mounting blocks to attach NASA wind instruments to mast
. Replacement sheet car sheeve halve - with a bearing
. Replacement winch handle grip
. Whisker pole end inserts to fit Allen pole ends
. Spreader mast feet
. Wheels to mount on the forward lower shrouds to prevent the genoa leach line velcro covers wrapping around the shroud when tacking
One really useful thing is to print templates and guides.
I generally use PLA, tho some parts have been done in ABS. Most parts fitted outside are painted for some UV protection, but this is the UK we are talking about. Strength wise, where a part is under load, in most cases it is compression so not really a problem and for something which is most like to have more load eg the replacement sheet sheave halve, I increase the number of walls and infill density.
The oldest parts are still in use after four years and the only parts which have failed are the shroud wheels, sometimes the sheet catches them and the twist in the vertical axis. Probably just need to make them a bit stronger.
I'm currently working on a replacement lower rudder bush. Once I have settled on the sizes then I can get a delrin one machined.
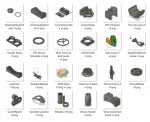
Chris
. Various switch mounts/plates
. Crockery, mug and storage container racks which can be stacked to make use of space
. Mounting brackets for things like the EDF1, the NASA LED mast top light and more
. Handheld VHF bracket
. Deck hardware standoffs
. Shaped mounting blocks to attach NASA wind instruments to mast
. Replacement sheet car sheeve halve - with a bearing
. Replacement winch handle grip
. Whisker pole end inserts to fit Allen pole ends
. Spreader mast feet
. Wheels to mount on the forward lower shrouds to prevent the genoa leach line velcro covers wrapping around the shroud when tacking
One really useful thing is to print templates and guides.
I generally use PLA, tho some parts have been done in ABS. Most parts fitted outside are painted for some UV protection, but this is the UK we are talking about. Strength wise, where a part is under load, in most cases it is compression so not really a problem and for something which is most like to have more load eg the replacement sheet sheave halve, I increase the number of walls and infill density.
The oldest parts are still in use after four years and the only parts which have failed are the shroud wheels, sometimes the sheet catches them and the twist in the vertical axis. Probably just need to make them a bit stronger.
I'm currently working on a replacement lower rudder bush. Once I have settled on the sizes then I can get a delrin one machined.
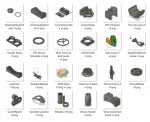
Chris