fulmarnyc
New member
I’m trying to disassemble my Whitlock Cobra (4 I believe) pedestal and I’m currently stuck at trying to remove the input socket from the top bowl. I tried putting the wheel back on the spindle and whacking it with a rubber mallet, it wouldn’t budge. I then tried heating the bejesus out of the socket with a MAP torch, still nothing. I’m not sure if the installer used adhesive instead of grease or it’s just totally locked in from corrosion but I have no idea what to do next. Any suggestions?
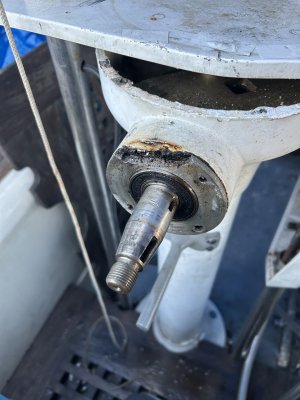
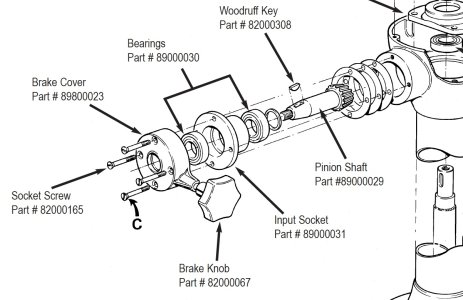
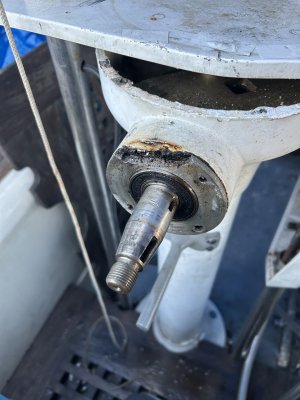
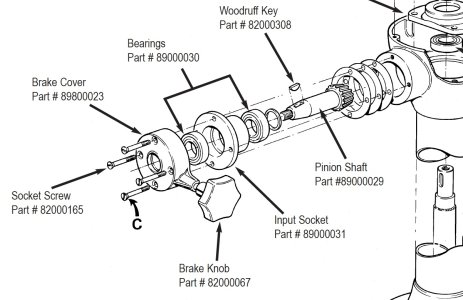